Geothermal Energy
A geothermal power generation plant is one of such avenues of engineering that meet the associated challenges by utilising the thermal energy stored in the earth to generate clean power. The energy acquired in the process, termed geothermal energy, has the highest baseload due to its independence of seasonal aspects (e.g., sunlight, winds, cloudiness). Despite such huge potential, different factors such as limited access to thermal resources, high capital costs, and operational risks during drilling of the geothermal wells have constrained its widespread development.
Current challenges
One of the main challenges is the need to drill to several kilometres depth to find reliable high temperatures, which is expensive and time-consuming. Drilling and completion make up a big part of geothermal project costs. Rig rental is a major expense, with drilling and putting casing taking up most of the time. Challenges like slow drilling and lack of awareness of the bottom of the hole result in non-productive time (NPT).
This industry particularly lacks digitisation and automation, relying on personal skills and manual data. Existing drilling systems are designed for hydrocarbon basins with oil-based muds, limiting their usefulness for geothermal and hard rock formations. Current systems are also based on rotary drilling, whereas the geothermal sector requires new technologies like percussion and non-contact thermal drilling.
There is currently no cost-effective way to accurately measure the forces and accelerations acting on a drill bit in a hard-rock geothermal well and to then transmit that information uphole to the driller in a timeframe that allows its use in optimising drilling performance. Consequently, drilling tends to be slow and drill bits suffer short lives, so geothermal wells tend to cost much more than oil and gas wells drilled to the same depth. If an accurate assessment of the dynamic state of the drill bit could be provided to a geothermal driller in near-real time, drilling parameters on the rig could be set to maximise the penetration rate and minimise bit damage in hydrothermal and Enhanced Geothermal System (EGS) wells. This would lead to cost reductions that are needed to improve access to the load-based power potential of geothermal resources.
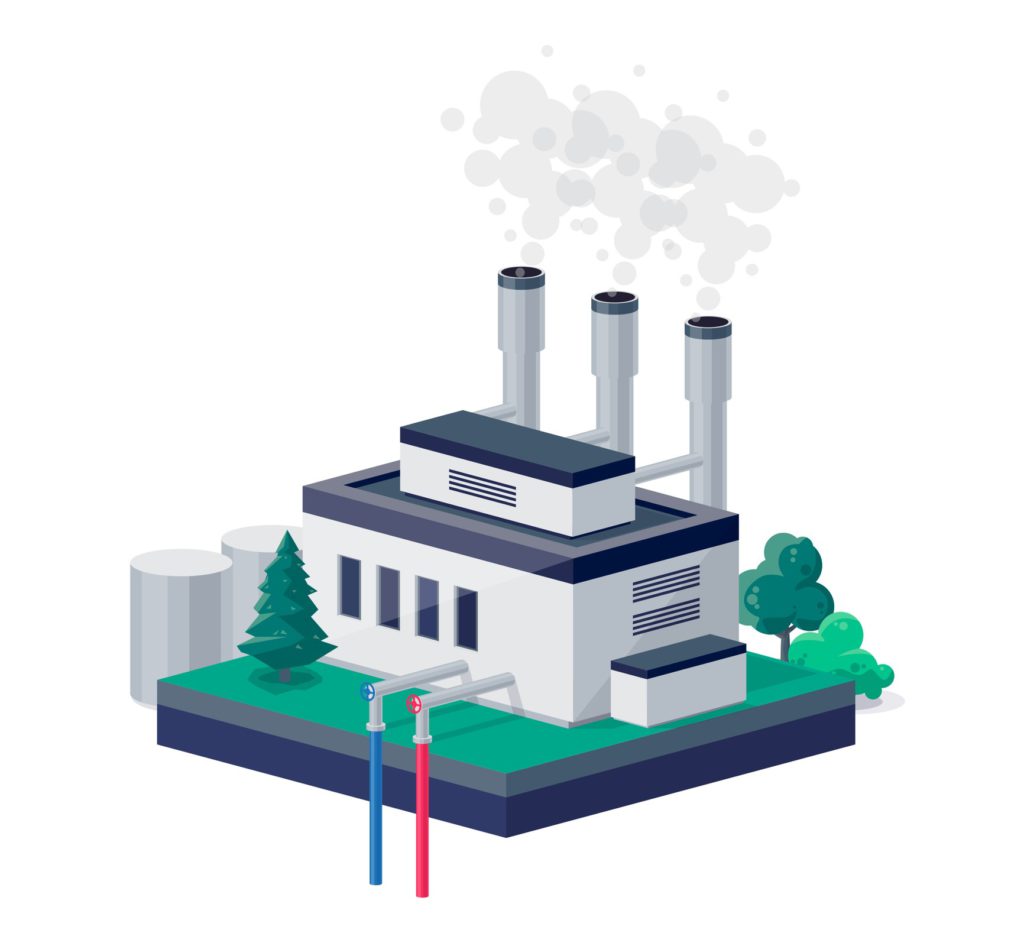
Contribution of Machine Learning (ML) and Artificial Intelligence (AI)
Traditional geothermal drilling approaches come with limited efficiency, accuracy, and safety. With the improvement of technology, Artificial Intelligence (AI) and Machine Learning (ML) are now known as powerful tools in geothermal drilling operations creating opportunities for innovation and optimisation in the geothermal industry. These innovative tools improve the accuracy and the cost of geothermal exploration, and optimise geothermal operations—driving down the overall cost of geothermal energy.
Out of many, machine learning and AI can help in resolving the geothermal drilling problems in the following three areas:
· Developing an enhanced monitoring system based on real time measurement while drilling (MWD) systems as well as acoustic and vibration sensors.
· Using an automated machine learning analysis method to predict drilling parameters, using a real-time monitoring and optimisation tool, as a unified system combining existing data and the newly developed methods, and finally, coupled drilling optimisation models to reduce overall geothermal drilling and production cost.
· Advice and support drilling operators in making informed decisions through real-time data, reducing many of uncertainties associated with drilling, which in term leads to less non-productive time (NPT), as the drilling can be more readily optimised to maintain good rate of penetration (ROP), borehole control and address possible drilling issues, before they could impact operation.
The OptiDrill have come to use ML to tackle the above-mentioned issues in drilling operations. The Optimisation of Geothermal Drilling (OptiDrill) concept was introduced to address and solve problems in drilling for geothermal resources that increases uncertainty and well construction costs. OptiDrill´s innovative drilling advisory system is based on a combination of enhanced monitoring systems, multiple data-driven ML modules, each being responsible for either analysis, prediction, or optimisation of one aspect of drilling or completion process.
The project is developing a drilling advisory system using artificial intelligence and novel sensors. OptiDrill solution will identify and recommend an optimum drilling solution that can be useful for geothermal, oil, gas, and many other industries working towards the net zero.

AI, ML and OptiDrill
Researchers have explored traditional machine learning techniques but a unified and reliable ML model based on the latest AI developments has not been developed. Despite many efforts to model drilling performance mathematically, it still remains complex and nonlinear.
That’s why OptiDrill and similar projects will use multiple ML model modules to create a drilling advisory system that analyses, predicts, and optimises different aspects of the drilling and completion process. To design an effective ML model for the OptiDrill system, a descriptive workflow was developed based on previous experience. The model is multi-modular, with each module’s development adjusted according to its output.
Proper handling, interpretation, and structuring of input data are vital for an ML model’s performance. The OptiDrill system uses a mixture of data mining, deep learning networks, and artificial neural networks to extract features from complex datasets and predict output accurately.
The manner in which the drilling bit is run is more important than which bit is run. OptiDrill coupled drilling optimisation ML models in the drilling advisory system will enable drillers to reach cost-effectively greater depths and higher temperatures on all types of geological formations for geothermal well drilling.